Emulsion Bitumen: What Is It and What Are Its Advantages?
Have you ever noticed the difference in road quality while driving? Some streets are smooth and allow vehicles to pass effortlessly, while others are bumpy and poorly paved. One key factor influencing the quality of these roads is the type of asphalt used, and bitumen plays a vital role as one of its main components. Beyond its use in asphalt, bitumen has various other applications. Understanding the different types of bitumen can help you make better choices for specific projects. But what exactly is bitumen emulsion, and what is it made of?
What Is Bitumen Emulsion?
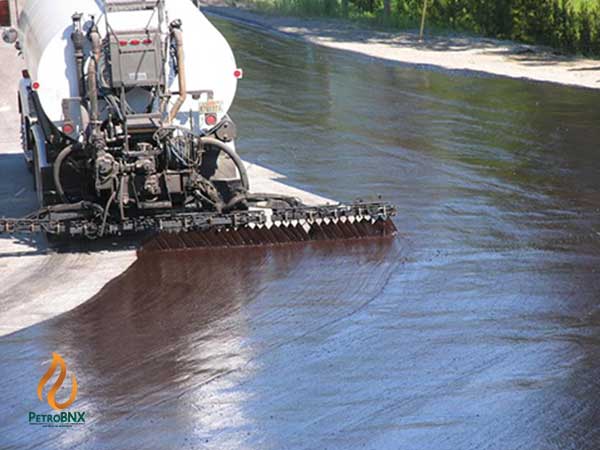
Bitumen emulsion is a specialized type of bitumen with a lower viscosity compared to traditional forms. It is produced by mixing bitumen with water and an emulsifier. The question What Is Bitumen often arises when exploring materials essential for infrastructure development.
This unique composition reduces its viscosity, making it more versatile and easier to handle than many other types of bitumen. Moreover, bitumen emulsion offers several advantages. For example, it can be stored and transported at lower temperatures, which reduces energy consumption and makes it a more environmentally friendly option.
How Is Bitumen Emulsion Made?
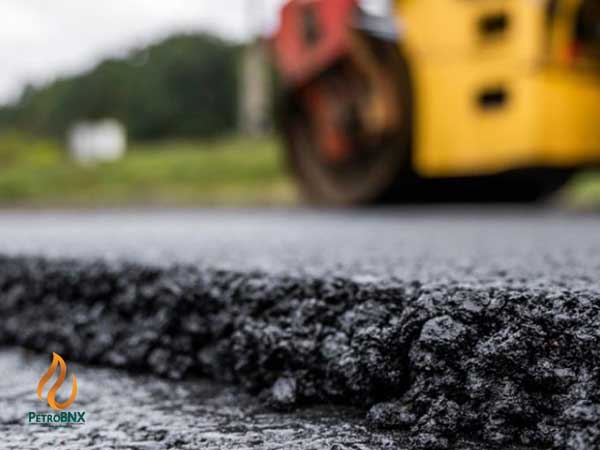
The production of Bitumen Emulsion is relatively straightforward despite its unique formula. The process involves three key stages: mixing, compounding, and milling. Here’s how it’s done:
1. Mixing Water and Emulsifier
The process begins by combining water with a specific type of emulsifier and additional chemical agents. The choice of emulsifier depends on the ionic nature of the chemical agents used, which determines whether the emulsion will be cationic, anionic, or non-ionic.
2. Compounding Water and Emulsifier with Bitumen
Once the water-emulsifier mixture is prepared, it is introduced into a device known as a colloid mill. Bitumen is then added to the mix. The proportion of bitumen varies depending on the intended application of the emulsion. For critical uses, the bitumen content ranges from 60% to 70%, while the average ratio generally falls between 40% and 70%.
3. Milling the Mixture
In the final stage, the colloid mill is used to break down the bitumen into tiny particles, some as small as two microns. While these small drops naturally tend to reunite, the emulsifier plays a dual role:
- Prevention: It creates a surface charge around the bitumen droplets to prevent them from merging.
- Suspension: It ensures the droplets remain evenly dispersed within the mixture.
After the milling process is complete, the bitumen emulsion is transferred to storage tanks for preservation and eventual use.
What Is Bitumen Emulsion Made Of?
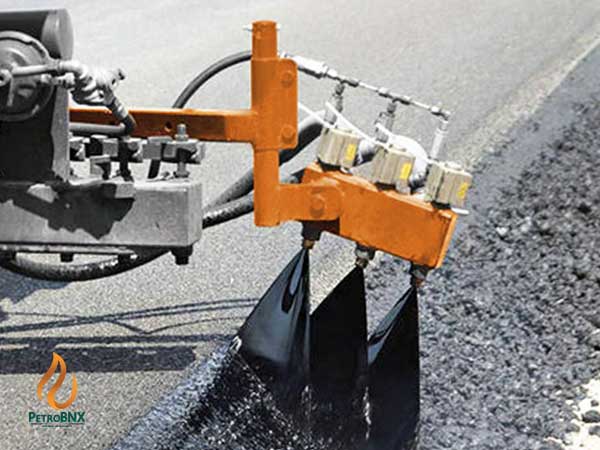
As mentioned earlier, bitumen emulsion consists of three main components: bitumen, water, and an emulsifier. The exact ratio of these components varies depending on the specific type of emulsion and its intended application.
1. Bitumen
Bitumen is the primary component, typically comprising 40% to 70% of the emulsion. The higher the percentage of bitumen, the more durable and adhesive the final product, making it suitable for heavy-duty applications.
2. Water
Water acts as the dispersing medium, accounting for 30% to 45% of the mixture. It helps reduce the viscosity bitumen, making it easier to handle and apply, particularly at lower temperatures.
3. Emulsifier
The emulsifier is a critical yet minimal component, constituting no more than 0.5% of the total mixture. Despite its small proportion, the emulsifier plays a crucial role by stabilizing the emulsion and ensuring that the bitumen particles remain suspended in the water. It also prevents the bitumen droplets from reuniting.
These carefully balanced components enable bitumen emulsion to deliver high performance while being cost-effective and environmentally friendly. Would you like to learn more about the different types of emulsifiers used or their specific roles
Temperature of Bitumen Emulsion During Production
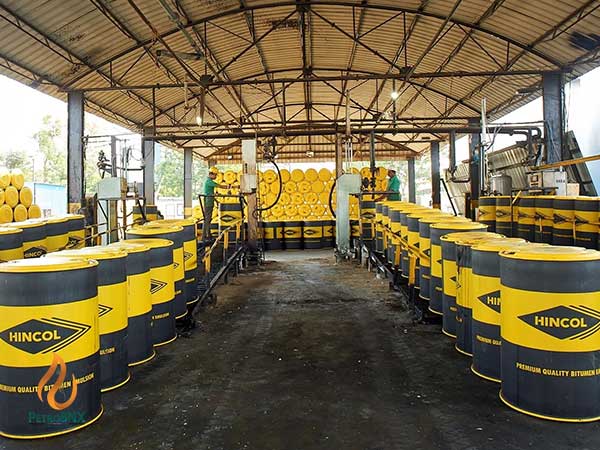
The temperature of bitumen emulsion is carefully managed throughout the production process to ensure the quality and stability of the final product.
- Molten Bitumen Temperature
When manufacturers introduce molten bitumen into the water-emulsifier mixture, its temperature typically ranges between 135°C to 150°C. This high temperature ensures that the bitumen remains fluid and can be properly mixed with the other components. - . Cooling During Production
As the production process continues, particularly during milling, the temperature gradually decreases. By the time the emulsion is fully processed and ready for storage, its temperature has dropped to approximately 95°C.
Bitumen Emulsion Standards
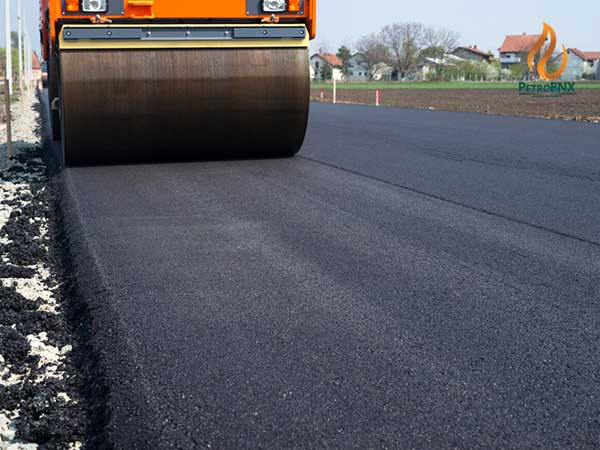
Bitumen emulsion products are evaluated and categorized according to specific standards established by prominent institutions. The two most influential organizations setting these standards are:
- The American Association of State Highway and Transportation Officials (AASHTO)
- The American Society for Testing and Materials (ASTM)
While many countries have their own regulations for producing bitumen emulsion, most align their standards with the guidelines set by these institutions. This ensures consistency and compatibility across international markets.
Key Factors for Categorizing Bitumen Emulsion
Bitumen emulsion products are classified based on several critical parameters. These include:
- Viscosity
- Determines the flow properties of the emulsion and its ease of application.
- Stability
- Refers to the emulsion’s ability to maintain its composition over time without separating.
- Breaking Time
- Indicates how quickly the emulsion breaks (i.e., when the water evaporates or separates, leaving behind the bitumen).
- Bitumen Content
- Specifies the percentage of bitumen in the emulsion, affecting its strength and performance.
- Particle Size
- Ensures uniform dispersion of bitumen particles, which impacts the emulsion’s durability and efficiency.
- pH Levels
- Helps identify the ionic nature (cationic or anionic) of the emulsion, which is crucial for specific applications.
- Temperature Sensitivity
- Assesses how the emulsion performs under different temperature conditions.
Key Factors in Grading Bitumen Emulsion
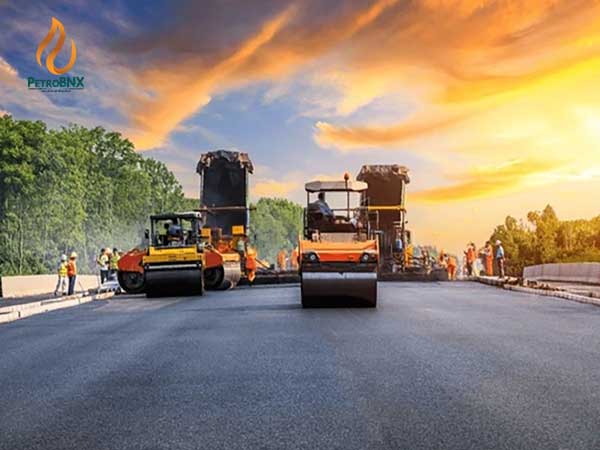
As discussed, organizations like AASHTO and ASTM grade bitumen emulsion products based on specific criteria, allowing buyers to select the right type of emulsion for their needs. These grades are determined by evaluating the following critical factors:
1. Bitumen Viscosity
Viscosity is one of the primary factors used to grade bitumen emulsion. It measures the fluidity of the emulsion, which depends on the proportion and distribution of bitumen in the mixture.
- Low Viscosity: Suitable for dense-graded aggregates as it flows more easily.
- High Viscosity: Ideal for open-graded aggregates due to its thicker consistency.
- Emulsions with smaller droplets and narrower particle distribution typically have higher viscosity.
2. Bitumen Ductility
Ductility measures the elasticity of bitumen emulsion and its ability to stretch before breaking.
- Testing Process: A ductility test involves stretching the bitumen until it breaks, with the breaking point indicating its flexibility.
- High Ductility: Emulsions with ductility exceeding 40 cm are suitable for heavy-traffic roads.
- Low Ductility: Unsuitable for heavy-traffic roads in winter, as they are more prone to breaking under low temperatures.
3. Bitumen Penetration
Penetration refers to the hardness or softness of the bitumen, determined by performing a penetration test using a standard needle.
- Hard Bitumen: Resists penetration and is ideal for use in hot climates, as it maintains its structure and resists deformation.
- Soft Bitumen: Penetrates more easily and is better suited for applications in cooler environments.
Bitumen Stability for Storage
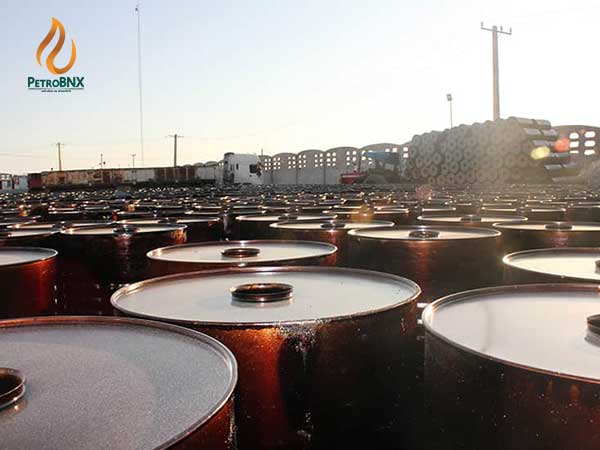
Bitumen emulsion stability, also known as bitumen sedimentation, evaluates the emulsion’s ability to remain consistent during storage without significant separation or settling of bitumen droplets. This property is crucial for maintaining the quality and usability of the emulsion over time.
Testing Process for Storage Stability
- Preparation:
- A sample of the bitumen emulsion is placed in a cylindrical container at room temperature.
- Observation Period:
- The cylinder is left undisturbed for 24 hours to simulate storage conditions.
- Sample Extraction:
- After the observation period, experts extract two samples: one from the top and one from the bottom of the cylinder.
- Weight Comparison:
- The weights of the two samples are compared. For the emulsion to pass the test, the difference in weight between the top and bottom samples should not exceed one unit.
This test ensures that the emulsion is stable during storage and does not experience significant sedimentation, which could compromise its quality.
Bitumen Particle Charge
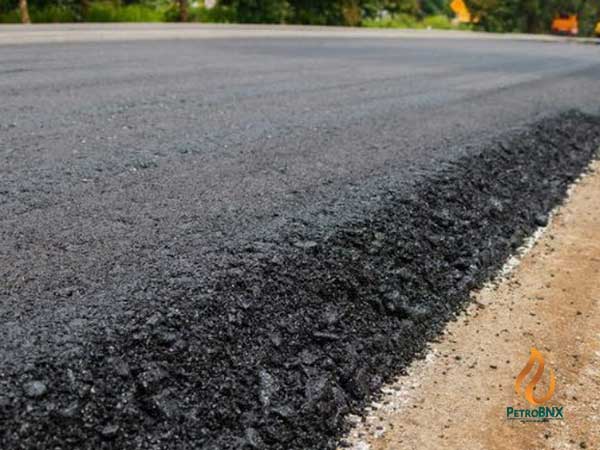
The particle charge of bitumen emulsion is another important factor in its grading. This property is determined by the surface charge created on bitumen droplets during production, which prevents them from reuniting. The emulsifier used in the process determines whether the bitumen droplets become anionic (negatively charged) or cationic (positively charged).
Particle Charge Testing
- Setup:
- A sample of the bitumen emulsion is placed in a container with positive and negative electrodes inserted into it.
- Application of Current:
- A direct electrical charge is applied for 30 minutes.
- Result Observation:
- The electrodes are examined for sedimented droplets:
- Droplets on the positive electrode indicate anionic emulsion.
- Droplets on the negative electrode indicate cationic emulsion.
- The electrodes are examined for sedimented droplets:
By determining the particle charge, experts can classify the emulsion’s nature, which is essential for selecting the right type of bitumen emulsion for specific applications.
What Is Bitumen Emulsion Used For?
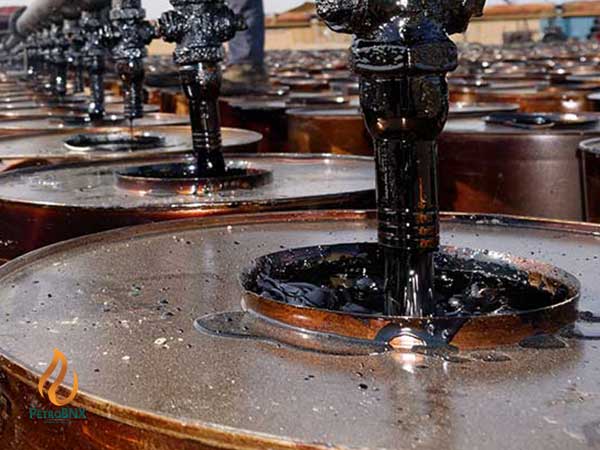
Historically, emulsions were primarily used for purposes like pesticide application. However, in modern times, bitumen emulsion has become essential in various construction and maintenance applications, particularly in road building and roofing. Below are some of its most common uses, especially in road construction:
1. Applying Tack Coats
A tack coat is a thin adhesive layer applied between two layers of asphalt to ensure proper bonding and extend the life of the pavement.
- Common Bitumen Emulsions Used: CRS-1 and CRS-2.
- Benefits:
- Improves asphalt quality.
- Reduces fatigue life of asphalt.
- Cost-effective.
- Application Temperature: Generally applied at 10 to 15°C.
2. Applying Chip Seals
Chip sealing is an affordable method to rehabilitate roads by applying a protective coating over old asphalt.
- Purpose:
- Protects asphalt from oxidation and aging.
- Reduces costs compared to building new roads.
- Applications:
- Ideal for light-traffic and rural roads.
- Preferred Material: Bitumen emulsion paints are widely used for this method.
3. Using Slurry Seals
Slurry seals enhance the cohesion of road surfaces by combining bitumen emulsion with aggregates and mineral fillers.
- Process:
- The mixture is sprayed onto asphalt to improve weather resistance.
- Uses:
- Prevents damage caused by bitumen oxidation.
- Ideal for minor road maintenance.
- Limitations:
- This method does not increase the structural strength of the roads.
4. Microsurfacing Method
Microsurfacing is an advanced form of slurry sealing, utilizing polymer-modified bitumen emulsion for increased strength and durability.
- Process:
- Dense-graded aggregates are mixed with polymer-modified emulsion.
- Applied to enhance road resistance to heavy traffic and harsh weather.
- Advantages:
- Stronger than standard slurry seals.
- Effective for more demanding road maintenance tasks.
Benefits of Using Bitumen Emulsion
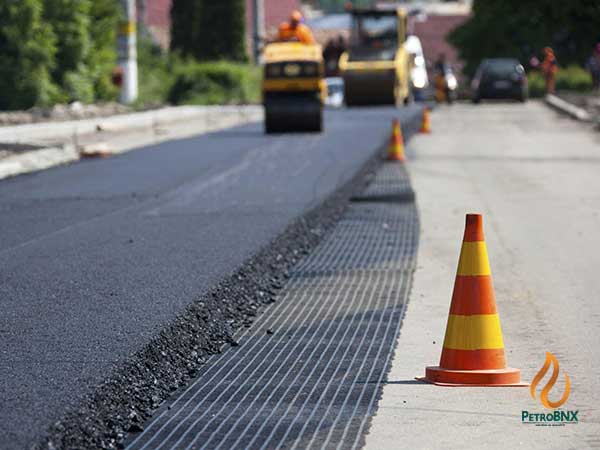
Bitumen emulsion stands out due to its unique composition and advantages, making it a preferred choice in many scenarios over other types of bitumen:
- Weather Flexibility: Since water is one of its primary components, bitumen emulsion can be applied in various weather conditions, including rainy days.
- Low-Temperature Application: It doesn’t require high temperatures during application, simplifying the process and reducing energy consumption.
- Ease of Use: Its composition makes it easier to work with compared to traditional hot-applied bitumen.
Bitumen Emulsion Adhesion and Versatility
- Strong Adhesion: Bitumen emulsion has anti-stripping properties, making it adhere strongly to asphalt.
- Versatile Applications:
- Widely used for asphalt paving.
- Can stabilize desert soil, preventing erosion.
- Eco-Friendly: Compared to traditional bitumen, it generates less waste during usage.
Disadvantages of Using Bitumen Emulsion
Despite its benefits, bitumen emulsion has limitations:
- Specific Usage:
- Not all types are suitable for every application.
- Their performance depends on categorization and specific functions.
- Temperature Sensitivity: The setting time is influenced by ambient temperature and grading.
- Storage Challenges: Prolonged storage or exposure to extreme temperatures can compromise its stability.
Quality and Composition of Bitumen Emulsion
The primary components of bitumen emulsion—water, bitumen, and emulsifier—determine its quality. However, variations in manufacturing can affect its performance:
- High-Quality Emulsion:
- Made with water or soap, ensuring strong adhesion and safe evaporation when applied.
- Low-Quality Emulsion:
- If gasoline solvent is used, toxic substances like sulfur may be released during evaporation, increasing health risks such as cancer.
Types of Bitumen Emulsion
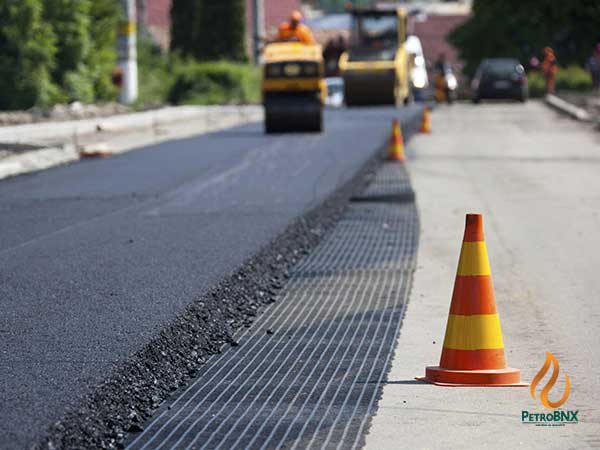
Bitumen emulsion is categorized based on particle charge and setting time:
- By Particle Charge:
- Anionic Emulsions: Names begin with “A.”
- Cationic Emulsions: Names begin with “C.”
- By Setting Time:
- Rapid-Setting: Evaporates quickly and is ideal for certain paving tasks.
- Medium-Setting: Has a moderate evaporation rate suitable for specific applications.
- Slow-Setting: Evaporates gradually, making it ideal for jobs that require longer working time.
Types of Bitumen Emulsion
- Rapid-Setting Bitumen Emulsion
- Properties: Evaporates and adheres to asphalt almost immediately after application.
- Examples: Cationic bitumen emulsion (CRS) and CRS-1.
- Uses: Ideal for creating road surfaces and applying cheap seals.
- Medium-Setting Bitumen Emulsion
- Properties: Produced by mixing bitumen emulsion with coarse, open-graded aggregates.
- Setting Time: Slower than rapid-setting emulsions, making it suitable for specific applications.
- Slow-Setting Bitumen Emulsion
- Properties: The most stable type of bitumen emulsion.
- Uses: Compatible with dense-graded aggregates, slurry seals, and recycled asphalt, providing flexibility for various applications.
Bitumen Emulsion Pricing
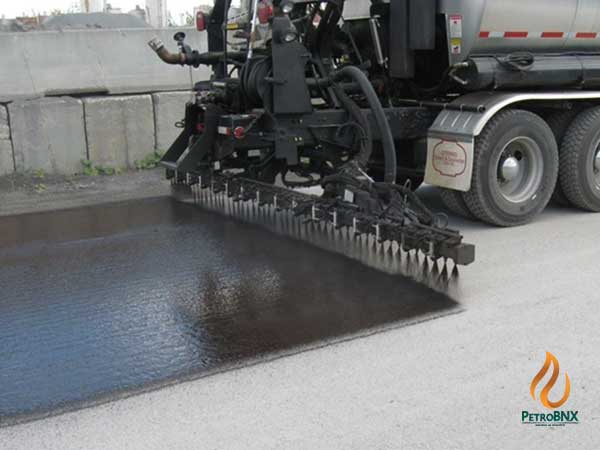
Several factors influence the cost of bitumen emulsion:
- Type of Bitumen:
- Cationic emulsions are typically more expensive than anionic emulsions.
- Raw Material Costs:
- The price of petroleum, emulsifiers, and other raw materials directly impacts pricing.
- Production Process:
- Variations in manufacturing methods also contribute to price differences.
Where to Buy Bitumen Emulsion
Quality plays a crucial role in the selection of bitumen for road construction and roofing. Understanding the types, benefits, and applications ensures you make the right choice. Among the various Bitumen Uses, waterproofing roofs and foundations stands out as a critical application.
For premium-quality bitumen emulsion, PetroBNX specializes in producing and exporting petroleum products. Contact us today to explore our range of bitumen solutions and receive the best offers tailored to your needs.
No comment